技術コラム
COLUMN
技術解説
研削焼け、研削割れとは
前回は、研削加工時における砥石への影響について解説しましたが、今回は製品への影響として「研削焼け」、「研削割れ」という現象について解説いたします。
1.研削焼けとは
以前、切削と研削の違いでも解説した通り、研削加工では切り屑の変形と砥石と工作物の摩擦による発熱によって、工作物の加工表層面の局部では600~1,000℃の高温になります。この研削熱のもたらす影響で、工作物表面を酸化させ着色するという現象を「研削焼け」といいます。研削焼けを起こすと、酸化膜が形成され、焼けの度合いで薄い褐色から赤色、青色へと色調が変化し、酸化膜の厚さも増します。研削焼けを起こした工作物は、外観上の色調も変化しますが、熱的な損傷で強度や耐久性などが劣り機械部品としての寿命を低下させます。
2.研削割れとは
研削割れとは、加工時に発生した研削熱が加工機の研削液によって急冷され、その衝撃で表面にクラックが生じる現象を言います。研削焼けでも解説した通り、加工表層面の温度は1,000℃近くにまで加熱されることから、炭素鋼等では結晶構造の変化する変態点温度まで達します。結晶構造の変化により体積変化が起こり、内部応力が蓄積して研削割れが発生します。
3.研削焼け、研削割れの対策
加工による研削熱を完全に無くすことはできないので、できるだけ熱の発生を抑えること、発生した熱をすばやく逃がすことがカギとなります。
1.適した研削砥石を使用
結合度(ボンド)が硬い砥石で重研削を行った場合は、目つぶれや目詰まりが起こりやすく、研削熱の温度が上昇するため研削焼けが発生しやすくなります。結合度の柔らかい砥石を使用することで自生作用を働かせることも対策の一つです。
2.適した加工条件
砥石の回転数が速すぎたり、送り速度が速すぎたり、過度な切込みは、研削抵抗が掛かる為、研削焼けが発生しやすくなります。砥石の回転数や送り速度、切込み量などの適した研削条件で加工することが重要です。
3.定期的なドレッシング
加工時間とともに鋭利であった砥粒の切れ刃は鈍化して切れ味が低下し、研削焼けを引き起こす原因となります。適度なタイミングでドレッシング(目立て)を行い、鈍化した切れ刃を鋭利な切れ刃に修正させることも対策となります。
4.適した研削液(クーラント)
発生した研削熱をすばやく逃がすことが重要となります。その為、砥石と工作物との加工点に、不足のないように適切な量の研削液を供給することで研削焼けの対策の一つです。また、研削液の種類は水溶性、油性に分かれます。一般的に水溶性の方が研削加工で多く用いられており、冷却性は優れていますが、潤滑性は油性に劣ります。それぞれ設備や加工条件、工作物の素材によって選定する必要があります。
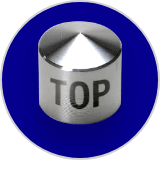